Floating wind turbines are crucial to the future of offshore wind, and to bring energy costs down to a competitive level, they require radically different thinking. French company Eolink is starting to build a full-scale demonstrator of its innovative pyramid-shaped floating wind turbine, which reduces materials and weight by more than 30%, and promises a big saving in energy costs.
As we’ve discussed before, the typical fan-on-a-stick pinwheel design used for onshore wind turbines isn’t a great fit when it comes to offshore, where most of the world’s best wind energy resources are found. When the water gets too deep to anchor a giant pole in the sea bed, you need to float your turbines. And when you try to do that using a pinwheel design adapted from land-based technology, you need an enormous amount of ballast material at the bottom. What’s more, they’re difficult and expensive to deploy and service, and the sheer physical strain imposed by a colossal fan mounted on one side of a nacelle means you need to run enormous bearings to take its formidable one-sided weight.
In our interview with Boston startup T-Omega back in September, the company described a different approach, something designed from the ground up for deep offshore deployment that could drastically reduce the weight, cost and engineering stress of a large turbine, while making it vastly easier to deploy and maintain. And while T-Omega is still searching for partnerships to get its designs past wave tank testing and into commercial use, it seems French company Eolink is well on the way to getting a similar idea off the ground.
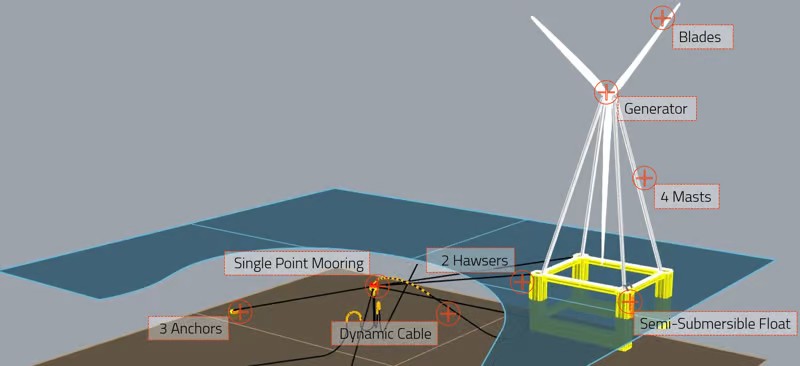
The key to this type of design’s advantages is its pyramid base, replacing the single pole of the pinwheel designs with a pair of triangles in much the same way as a ferris wheel is suspended. Straight away, the massive weight of the huge fan is distributed evenly between bearings at both ends, rather than just one. So the nacelle at the top can be lighter, and instead of a single, monolithic pole, you can run four much slimmer supports as a pyramid shape. This greatly reduces weight, and it also gives you a wide base at the bottom as opposed to a single point, so there’s much less need for heavy ballast metal to keep the thing upright.
You can’t use these ferris wheel pyramid designs on land, because land-based turbines need to be able to tilt themselves into the wind to maximize their output. That’s not a problem in the deep ocean; you simply tether these floating pyramids to the bottom. Whichever way the wind blows, the turbine gets blown in that direction, and with the tether mounted to the front side, it always ends up facing the wind.
While wind direction and ocean currents are usually aligned in the deep ocean, Eolink says it’s designed a dynamic ballast system that can steer the turbines up to 120 degrees when the two are misaligned. This also lets the operator divert the wake left behind each turbine, potentially sacrificing a little power from the front row of turbines in order to maximize output from the entire wind farm.
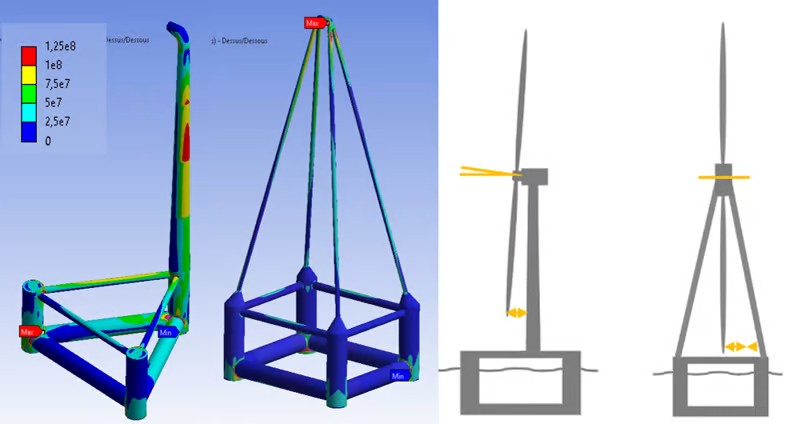
In terms of building and deploying these machines, everything’s simply much easier. They can be built at a shipyard and deployed straight into the water, where they float in relatively shallow depth thanks to the fact they’re not carrying massive amounts of ballast under the waterline. Eolink says a single shipyard facility should be able to pump out 67 turbines a year.
Once built, you pop them in the water and tow them out to your site, tether them, connect them up and you’re off and running. No specialist multi-million-dollar-a-day crane ships are needed for deployment or maintenance because you can just tow them back into port and do your work there where it’s vastly easier and cheaper.
So between materials, engineering, build, deployment, scale and lifetime maintenance, these designs should have a cost advantage every step of the way. And with the European offshore wind segment struggling in the face of rising materials costs, inflation, supply chain issues and pressure from Chinese companies that are beginning to ramp up their global offerings, these advantages could be absolutely critical.
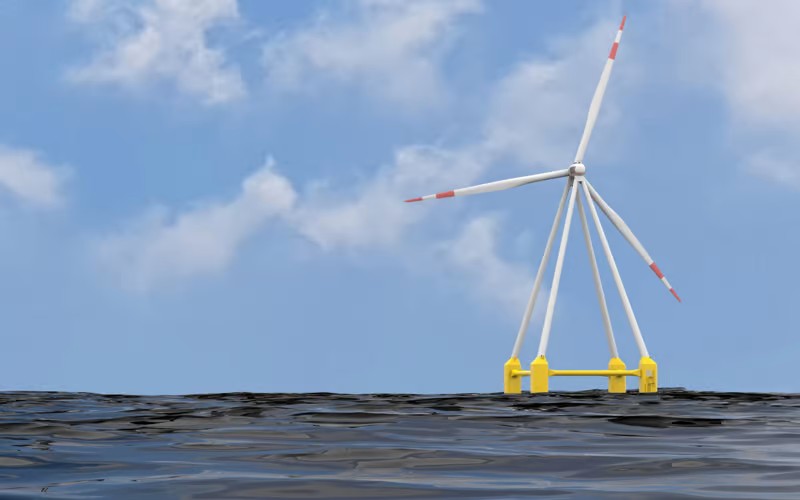
According to the good folk at Recharge News, Eolink has received a Final Investment Decision (FID) thanks to new investments from Spain’s Acciona Energy and project management firm Valorem. Now fully funded to the tune of US$23 million, Eolink is moving to begin the manufacture of a full-scale test turbine, to be deployed at the SEM-REV test site in the French Atlantic ocean.
This 5-megawatt demonstrator will weigh 1,100 tons, with a square base of 52 m (171 ft) per side. The rotor itself will have a 143-m (469 ft) diameter. Eolink says its design should use more than 30% less steel than a traditional pinwheel for the same rated output. Because the blades no longer risk hitting the tower, longer and more flexible blades can be installed for a given tower height, resulting in an estimated 10% more energy output from the same wind conditions. Construction is beginning this month, it’s expected to be moored and anchored in place by the next (Northern Hemisphere) spring, and it’ll be commissioned in 2024.
Even better, the company says it scales considerably better than pinwheel-style turbines. Indeed, it’s got plans for a monster 20-MW turbine using this design. That’d be considerably bigger than the world’s current largest wind turbine, which itself is absolutely mammoth in scale.
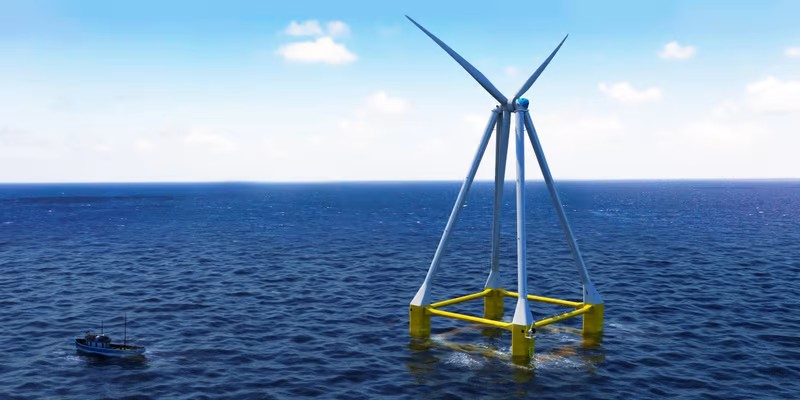
In terms of the bottom dollar, Eolink says it expects these machines to deliver electricity at between 20-25% more cheaply than “a reference technology.” So it’s not the radical 50% price cut that T-Omega and more extreme solutions like World Wide Wind’s dual contra-rotating vertical-axis wind turbines promise, but it looks like these French turbines will be out there in commercial-scale testing a lot sooner. Interesting stuff, we look forward to seeing how they perform.
Source: New Atlas
Recent Comments